로터스는 설립 초기부터 경량화를 통한 성능 향상을 꾀했다. 경량화로 성능을 높인다는 것은 시대를 앞선 컨셉트였고 지금에 와서는 그 중요성이 더욱 강조되고 있다. 절정에 달한 내연기관의 효율 향상 보다는 경량화의 여지가 더 남아있기 때문이다. 하지만 문제는 비용이다. 무게를 줄이는데도 많은 돈이 들어간다.
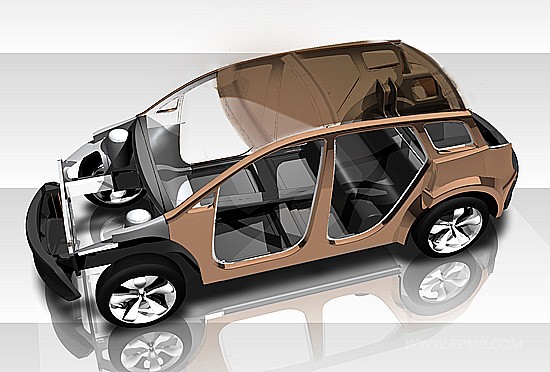
로터스의 자회사 로터스 엔지니어링은 일반 양산차에 경량화 적용 시 얻을 수 있는 효율 향상과 비용을 조사했다. 이번 조사는 ICCT(International Council on Clean Transportation)와 합동으로 진행했으며 경량 소재의 사용과 효율적인 디자인 등에 초점이 맞춰져 있다. 이번 조사에 사용된 모델은 토요타 벤자였다.
로터스 엔지니어링의 조사에 따르면 파워트레인을 제외한 벤자의 무게를 38% 덜어낼 경우 발생하는 부품 비용의 증가는 3% 정도에 불과하다. 물론 당장은 아니고 2020년 정도에 상용화가 가능한 것으로 알려졌다. 2020년 출시를 목표로 개발되는 새 플랫폼은 고강성과 경량을 만족하는 소재가 어우러진다.
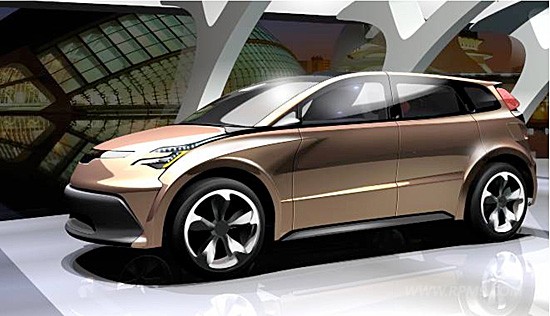
미국의 DoE(Department of Energy)의 조사에 따르면 차량 전체 무게를 33% 줄일 경우 연비는 23% 상승한다. 그만큼 경량은 친환경과 밀접한 관계가 있다. 로터스는 경량 아키텍처와 이피션트 퍼포먼스 두 가지 컨셉트를 제안하고 있으며 이는 미국의 NHTSA(National Highway Traffic Safety Administration)와 EPA(Environmental Protection Agency)로부터도 인정을 받았다.
로터스 엔지니어링은 2017년과 2020년 출시를 목표로 두 가지의 시나리오를 준비했다. 첫 번째는 경량 소재를 현재의 생산 공정에 적용해 무게를 줄인다는 계획이다. 파워트레인을 제외하고 차체 중량을 21% 줄이면서 비용도 2% 절감할 수 있다. 로터스 엔지니어링은 기존의 실내 공간과 안정성을 그대로 확보하면서 무게를 줄일 수 있다고 밝혔다.
현재 벤자의 보디-인-화이트는 총 400개가 넘는 부품으로 이뤄져 있다. 하지만 2020년 플랫폼을 적용할 경우 보디 부품의 수는 211개로 줄어든다. 보디에는 플로어와 언더보디, 대시보드, 범퍼, 루프 등이 포함된다. 현재 벤자 보디는 100% 스틸이지만 2020년 플랫폼에는 알루미늄이 37%, 마그네슘이 30%, 합성 소재가 21%, 고장력 강판이 7% 함유된다. 이럴 경우 보디의 중량은 382kg에서 42% 감소한 221kg이 된다. 앞뒤 범퍼도 스틸 빔을 알루미늄 빔으로 대체해 11kg을 줄이지만 기능은 그대로 유지된다. 전체 파워트레인의 무게는 410.4kg에서 13.2% 감소한 356.2kg까지 떨어트릴 수 있다.
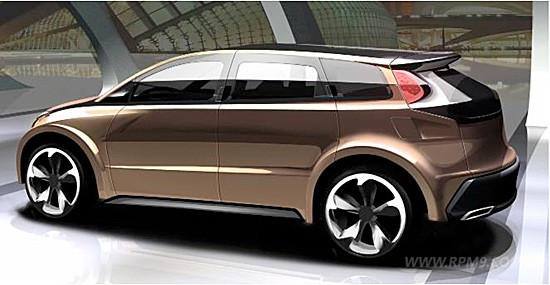
거기다 공정에 필요한 에너지 소비를 줄이고 빠르게 생산할 수 있는 기술도 개발 중이다. 로터스 엔지니어링은 이미 이 같은 공정이 소량 생산 모델에 적용된다고 밝혔다. 에너지 소비가 적은 용접과 접착 본딩 등은 엘리스 등의 로터스 모델에 적용돼 높은 품질을 인정받고 있다.
펜더와 도어도 벤자는 100% 스틸이다. 이를 마그네슘(33%), 플라스틱(21%), 스틸(18%), 알루미늄(6%)로 대체할 경우 전체 중량은 143kg에서 84kg으로 41% 감소한다. 2020 플랫폼에서는 에어컨 모듈도 콘솔로, 냉난방 기능의 컵홀더는 공조장치 모듈로 통합된다.
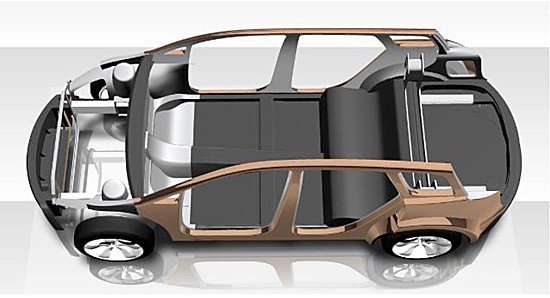
차량에 적용되는 유리도 경량의 여지가 상당하다. 일반적으로 윈드실드의 두께는 4.5~5mm 사이이고 무게는 13kg 내외이다. 이 두께를 2.6mm까지 낮추면 경량화는 물론 무게 중심도 낮출 수 있다는 장점이 발생한다.
프런트 시트의 경우 기존의 마운팅 브라켓을 제거해 10kg을 덜어낸다. 대신 부분적으로 플로어팬을 강화해 떨어지는 강성을 보완한다. 이럴 경우 시트의 전체 중량은 절반으로 감소한다. 탈착 가능한 4개의 카펫 모듈을 적용할 경우 비용을 절감하면서 카펫의 품질 향상도 기대할 수 있다. 2017 플랫폼 기준으로 인테리어 중량은 250kg에서 182kg으로, 2020은 153kg까지 떨어진다.